Starting an advanced reactor industry
Thoughts on moving from one-of-a-kind demos to fully fledged industry
As explored in depth by Stephen Ezell at ITIF, China is surpassing the U.S. and Europe in nuclear technology, and in order to compete, we may need a “whole of government” approach. To reestablish advanced reactor leadership, we need a long-term strategic vision that accounts for the specific challenges and opportunities of advanced reactors. Further, we need to lay the groundwork to create an entirely new industry, with new supply chains, business models, and technology, not just develop one-of-a-kind projects. What follows is inspired by the history of advanced reactor development and our own efforts to develop novel nuclear power technology.
Advanced reactor history: still on the way to 2nd-of-a-kind
Metal cooled reactor history
The first “usable” electricity from nuclear power was from a liquid metal cooled reactor, the Experimental Breeder Reactor I. Liquid metal reactors have used mercury, sodium, sodium-potassium eutectics, lead, or lead-bismuth eutectics to cool the core instead of water.
While these concepts showed promise, they have yet to scale. The closest it came to serial use was in the Alfa-class submarines in the Soviet Union, but they faced several challenges. The coolant was a lead-bismuth alloy, and the reactor design was technically compelling with higher operating temperatures making it more efficient and giving it a higher power density. However, the reactors were very difficult to maintain. Out of seven built, four had major issues, and the remaining units were all eventually decommissioned (if sinking to the ocean floor counts as decommissioning…).
Outside of these submarines, liquid metal reactors have mostly been one-of-a-kind projects. The U.S. built ~6 liquid metal reactors, none of which were commercial successes. France has a long term (multi-decade) reactor development program that stared with Rapsodie in the 1960s, then built Phenix, and finally Superphenix in the 1980s. France had intended to continue with another one-of-a-kind project, ASTRID, but this project was unfortunately cancelled in 2019. Russia has been working on the BN series reactors which have evolved from 5 to 800 MWe over 5 reactors and 50 years. The goal is that the BN-1200 will enter into “serial production” after demonstration in the mid-2030s.
The point here is that to develop an advanced reactor into a product ready for “serial production”, it took Russia 5 demonstration reactors over 70 years.
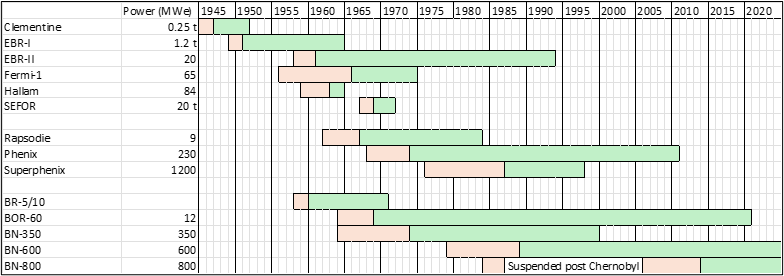
Gas cooled reactor history
Gas reactors were similarly explored in the early days of the industry. There have been reactors cooled with air, CO2, helium, and nitrogen. Several countries, including the United Kingdom, China, France, Germany, and the U.S., explored gas reactors through various research programs.
The first gas-cooled reactors in the UK, France, and the U.S. were simply air-cooled graphite piles. Examples include GLEEP (UK), G-1 (France), and CP-2 and X-10 (US). These later evolved into fully fledge reactor programs, but similar to the liquid metal reactor history, each reactor was a one-of-a-kind project. Even reactors carrying the same title, such as the AGRs were vastly different in internal architecture and engineering.
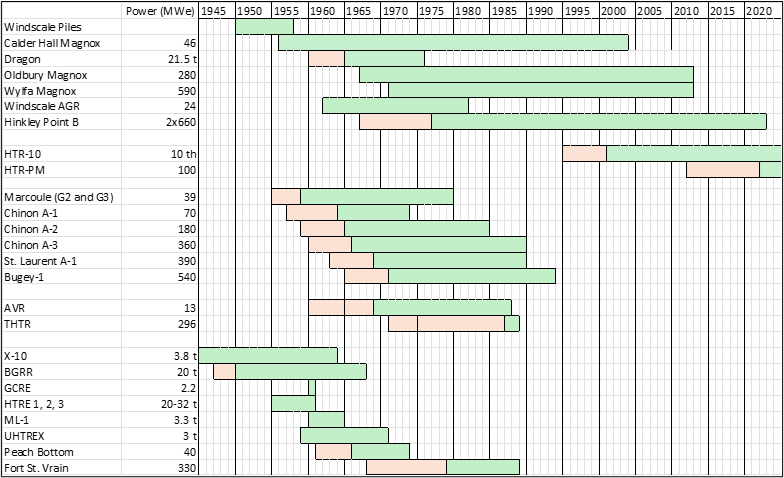
Other advanced reactors, like molten salt reactors, have not had the attention and deployment of gas and metal cooled reactors. The Molten Salt Reactor Experiment in Oak Ridge operated for 13,000 hours or less than two complete years. No scaled-up versions followed, although Oak Ridge did estimate the next demonstration reactor required for molten salt reactor development would have cost $2.5B in 2024 dollars.
We made these timeline charts to show just how much the industry was building and testing, and despite all of these efforts, light water reactors were still the only commercial success. If we want an advanced reactor industry, we need a similar level of building and testing.
Focus for the long-term
Success requires a long-term focus. Engineering is challenging, and the long-term view sharpens focus on solving the problems of today without diversion. In advanced reactor programs, apparent shortcuts can distract engineering teams when they are facing challenges. For example, the Next Generation Nuclear Plant program (NGNP) shifted internal focus to study printed circuit heat exchangers (PCHE) when facing the challenges of manufacturing large helical coil steam generators (HCSG). PCHEs have many attractive attributes, but there is no ASME code approved pathway to using them in nuclear reactors today. One could argue that the NGNP team should have focused on developing HCSG manufacturing capability which have better positioned the industry today as X-Energy is planning to use an HCSG.
The global reactor development experience shows us that going from concept to commercial takes at least 20 years with several prototype reactors along the way. Even still, after decades, these programs often shift focus to a new design or get cancelled. We are convinced that a focused, well-funded, multi-decade (less depending on funding) effort will be required to break this pattern and create an advanced reactor industry. This is what Idaho National Lab was built for!
Creating an industry, not a prototype
Creating an industry is much more than designing a reactor. We need new manufacturing capability, new fuel fabrication lines, novel regulatory approaches, new business models, suppliers for components, parts, services and more. The good news is that there are many startups in this space, and their collective capital and drive is larger than any one company’s drive could be. Third Way’s Advanced Nuclear Map shows 130 projects worldwide, and the slide below from the NRC shows over 30 in the U.S.
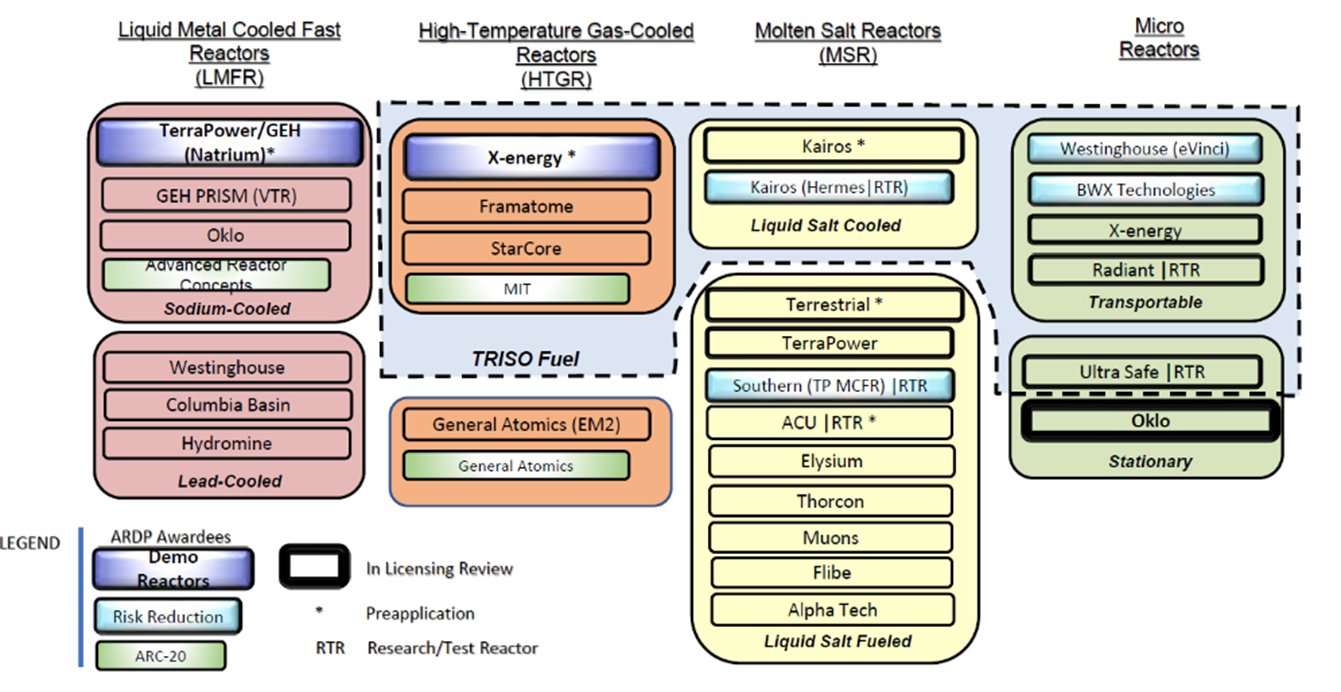
When focused on MIGHTR, we made the calculated decision that the outsized number of HTGRs among advanced reactor developers would be to our benefit – helping to seed the development of all parts of the necessary industry. We intentionally carved the <20 MWt range out of our original MIGHTR patent because we knew it would be useful if someone else was developing similar technology. For example, we faced several technical challenges, where we would have benefited from someone’s success:
Helical coil steam generator manufacturing
Printed circuit heat exchanger ASME code case development
Helium circulator development
Vessels, seals, and large-scale helium containment
Auxiliary tooling and robotics
The technology and regulatory success from ongoing HTGR projects will benefit the whole industry, and it could be a major turning point for HTGRs in the U.S. Success for the larger players is likely to help the early-stage companies as well.
How the advanced reactor industry can move faster
There are several forces already accelerating the creation of an industry:
The highest level of public support for nuclear in decades is creating new policy opportunities and easing siting concerns.
The Advance Act may create more industry and regulatory willingness to innovate in a way that accelerates deployment.
Risk informed licensing, either through the Licensing Modernization Project (Reg Guide 1.233) or 10 CFR Part 53, may create the environment for innovative safety cases or regulatory approaches, which may simplify licensing, development, and construction.
However, the advanced reactor community can likely move faster than it is, so it is useful to identify some of the forces that slow its development:
Total cost to design and engineer a novel power plant system is in the billions of dollars. Look forward to a future post on this topic.
Complex system integration creates project management challenges. These aren’t specific to nuclear. The extensive supply chain for the Boeing 787 was notorious for causing delays. SpaceX has had great success with vertical integration. Westinghouse’s tried to resolve some construction cost overruns at Vogtle and Summer through an acquisition of CB&I Stone & Webster. Just look at how extensive the TerraPower list of suppliers is.
Aversion to regulatory risk and licensing uncertainty. Design engineers see rejection as too high a cost to pay late in a project, so they design-in conservatism that sometimes is unnecessary. This can materialize in several ways: refusal to adopt a new code or method or assuming an LWR safety system is necessary for an advanced reactor, when in both cases the NRC has shown themselves to be innovative and flexible. However, there may be other cases where the extra conservativism was necessary to deal with licensing uncertainty that stemmed from early design uncertainty. This licensing uncertainty does not necessarily come from the NRC. It also comes from the inherent complexity in the design process internal to the reactor design organization.
On the integration, Kairos Power is vertically integrating to resolve this challenge, but others in the space are relying on a host of suppliers, so management will be key to their success. There is a lot of room for software development of configuration management tools to integrate suppliers.
On the regulatory risk, the nuclear community has an interesting culture of innovation. There are many advanced reactor startups bringing new ideas into the industry. However, their willingness to use different tools, license new materials, license new manufacturing methods, or present new safety cases to the regulator has been limited. In many of these areas, there is a huge reward for successfully delivering something novel, but also a huge risk of wasted time and money if you fail to deliver. Firms likely need to shield engineers and managers from the risks or reward them explicitly for the wins to encourage a new culture of innovation.
How to do tech selection
Selecting which projects to fund that maximize the industry’s success is a critical piece of the puzzle. The capital for developing advanced reactors should concentrate around the best advanced reactor projects which means we need methods for assessing the “best projects”. These selections should happen based on TRL, cost to deploy today, team capacity/credibility, market potential and other benefits.
Market potential can be assessed by considering the realistic market this technology could serve in the next 20+ years. This comes from identifying what markets could need nuclear power on that timescale. Process heat is a good example here.
In our view, technology readiness should be evaluated based on both past and present developments. While recent advancements might accelerate the maturation process, it is unlikely that any breakthrough in energy will enable the development and deployment of full nuclear technology, such as ARs or SMRs, at more than twice the historical rate. Considering that Water-Cooled Reactors took 40 years to mature in construction and operation, we estimate a timeframe of at least 20 years to achieve technological maturity and near-full economic potential from scratch. Technologies further along the development path may require less time, but this needs to be carefully judged for technology selection.
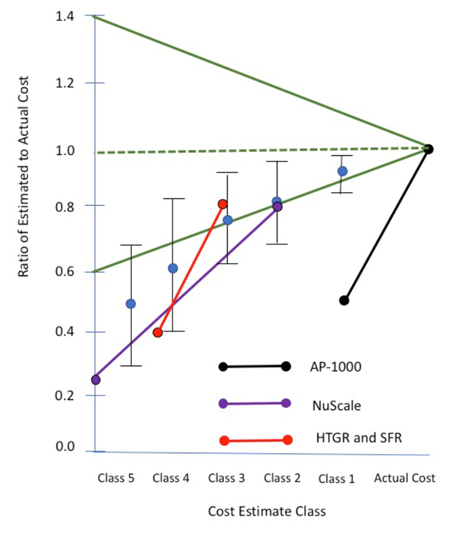
Estimating the cost of deployment today is complex. Detailed cost and timeline projections are not feasible until a design is fixed and detailed. However, high-order cost modeling techniques, based on footprints, building volumes, and main components, can provide preliminary estimates. It is crucial to remember that a cost estimate can only be as accurate as the design it is based on. Designs with attractive cost estimates but low TRL and early-stage plant designs are likely to be misleading. To mitigate this, we proposed a “develop by embodiment” strategy, as published in ANS, which significantly reduces the risk of unexpected design growth and cost overruns from the early days until the design is complete.
Because early cost estimates often underestimate final costs, the industry should explore low(er) cost pathways to increase the accuracy of these modeling efforts. One option is increased non-nuclear system demonstrations to prove manufacturability, constructability, and operability. This can be coupled with an independent design review on licensability. Together, this could get a reasonable look at the comparable costs between different technologies without requiring expensive FOAK nuclear projects.
Concluding remarks
Advanced reactors will face many of the same issues that light water reactors do, and there is a lot of knowledge and experience to share between the communities. There are a few key elements we observe in other countries with healthy advanced reactor programs:
A thriving light water reactor industry
Russia has 20 VVERs under construction globally
China has 17 total HPR1000s and CAP1000 under construction
Long term funding continuity over decades.
Technical focus on bringing a single reactor type to completion before pivoting.
Paired with wise technology selection, we believe there is a path to a thriving advanced nuclear industry.
Good of you to point out that the nuclear industry is in this together and will benefit of each other's successes.
This is why e.g. Westinghouse's legal threats to KHNP over old licence issues are self destructive. There aren't many AP1000 customers because the Western nuclear industry has not performed well in the last 20 years, not because of competition from KHNP. The only way to get new customers is by someone showing that you can build NPPs in the 2020s in time and on budget. The more vendors try, the higher the chance someone succeeds.